October 7, 2020
Whirling Machine Series – Part Two
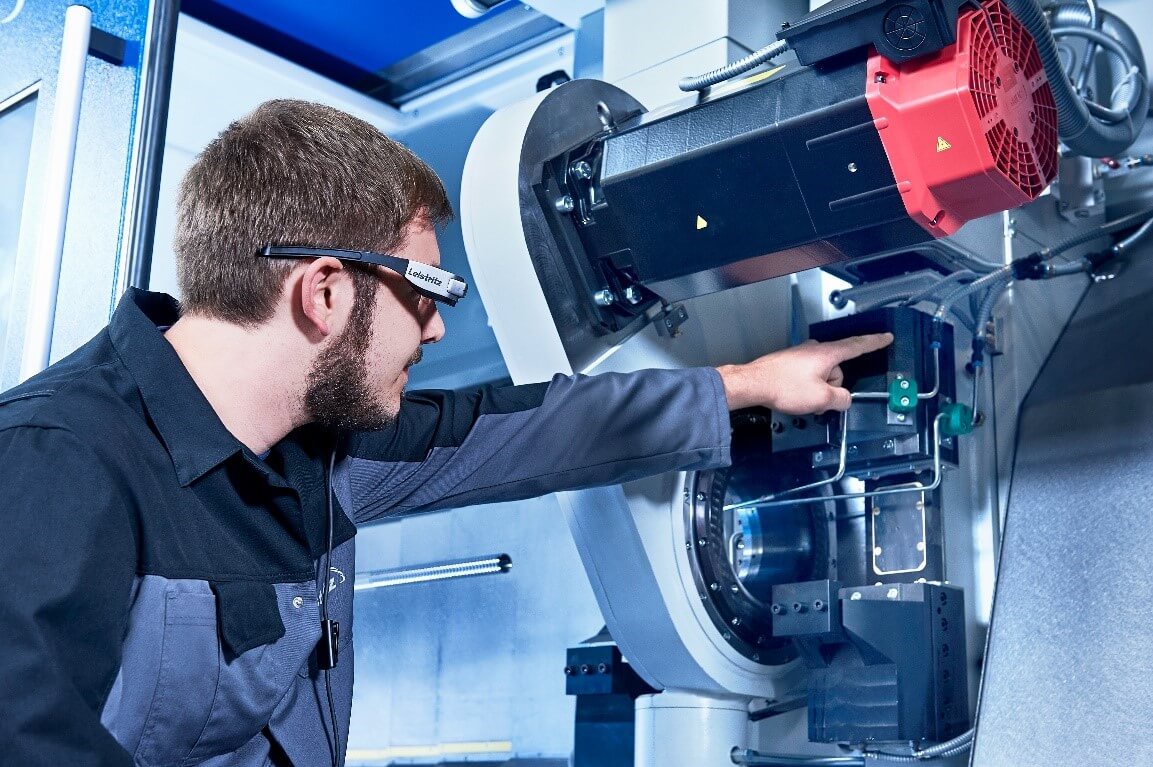
In a four-part blog series, we will discuss profitability, technical possibilities, applications, innovation, environmental protection, and market development of whirling machines.
With ball screw spindles, EPS screws, and similar rotationally symmetrical workpieces, high precision and controlling costs are essential to the whirling process. Todayβs modern whirling machines coupled with a dry cutting process can manufacture these components so precisely, it eliminates the need for grinding. This advantage addresses the high costs associated with grinding in favor of a more modern, cost effective whirling technology.
Today ball screw spindles and worm gear shafts can be found in large numbers in production plants and consumer products. A ball screw drive, for example, moves production line tables for cell phones and other microelectronic products from station to station. In automobiles, worm gears are part of Electrically Power Steering (EPS) units.
Application areas for rotationally symmetrical screws have been increasing and so have the quantities that are required. It is only logical that screw component manufacturers explore the latest technology advancements in manufacturing and adopt processes to take advantage of the large cost savings that dry high-precision whirling provides.
Cycle Time Savings
Reducing the throughput time of a workpiece is one of the most important economic factors – especially in mass production. Switching to a faster process or being able to eliminate an entire production operation is a massive cost-saving step.
Since whirling is a special form of milling, it has the advantage that a large amount of material can be removed quickly with its geometrically determined cutting edges. The inset edge produces short, comma shaped chips that carry away most of the heat generated by the cutting action leaving the part cool to the touch. Grinding as an alternative production method and produces small particles, therefore removing them much more slowly.
When it comes to accuracy and surface finish quality, grinding has been the go-to process of choice, especially in hard materials. Advancements in the case of precision whirling, components can now be manufactured in a single pass to the required finish quality, therefor eliminating the typical costly second step process of grinding or honing. Today the super hard material known as (CBN) is used in many hard-part turning and milling applications, is now used in whirling.
Environmental Benefits from Whirling Process
“Whirling” has become a finishing process that combines the advantages that come from the speed of milling and precision of grinding. Compared to grinding, cycle times are considerably reduced and a typical workpiece can be machined six to seven times faster with whirling machine. In addition, a whirling machine can manufacture an entire workpiece in a single clamping thus eliminating the time-consuming process of unclamping/re-clamping and lead pickup to produce a part.
Operational Savings
Tooling costs are a huge consideration, as they are substantially lower for turning and milling then for grinding. This is also true for whirling but the potential cost savings associated with coolant makes up for the cost of tooling.
With grinding, there is no avoiding the use of cooling lubricants because of the high cutting performance. These fluids must to be pre-purchased and stored on-hand. Chemically there are problematic substances that require careful handling in order to protect the employees and the working environment.
After using coolant during a grinding operation, it must be filtered and then cooled by a separate unit before going back into circulation. However, the processing and disposal of the cooling lubricant after its expiration is time-consuming and expensive. A large portion of the remaining filtered residue (grinding sludge) is classified as hazardous waste. To further reduce the amount of hazardous waste produced, a sizeable capital investment is required for equipment to handle this material. This process is known as briquetting and is used to compress the grinding sludge into pucks to provide easier handling; however, the scrap still must be disposed of.
By using whirling and its dry cutting process, these costs and additional steps do not exist. The machine can be cleaned dry, which only takes a fraction of the time. Additional savings is also realized since the metal shavings are not considered hazardous waste and can be recycled directly as valuable raw material.
The energy consumption linked to precision whirling is significantly lower. This is due to the elimination of additional coolant handling equipment and the significantly shorter cycle times. With the constantly rising energy costs and the political objectives to reduce the carbon footprint is an issue for every company.
Purchasing and Space Savings
The capital investment for industrial production machines requires a strong Return On Investment (ROI). With investments in the six- to seven-digit range, purchasing a machine is a commitment to a long-term machining process.
A typical whirling machine cost is slightly more than a grinding machine, but a whirling machine can replace several grinding machines because of faster operation. Hard machining eliminates manufacturing steps and personnel expenses, and throughput times are significantly reduced.
By eliminating the coolant and the additional processing equipment needed makes whirling a more compact solution. As a result, both the shop floor production area and storage area inhabit a much smaller footprint.
It is this entire range of economic advantages that illustrate how modern precision whirling can technically replace grinding. Savings opportunities and competitive advantages are key in the growth market for components with helical geometry. Today, users of EPS worm and ball screws such as those being developed for autonomous vehicles and aircraft, are considering manufacturing these components in-house and have become less dependent on suppliers.