March 21, 2020
Pumps in Transfer and Pipeline Service
Twin-screw Pumps
Twin-screw or three-screw pumps are often used in crude oil pipeline services. Three-screw pumps can boost pressure from laterals to the main trunk lines, while twin-screw pumps are predominantly used in the main line boosting stations.
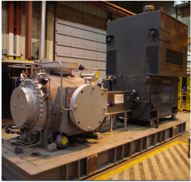
The primary advantages of screw pumps in pipelines are their ability to handle a wide range of viscosities, where centrifugal pumps will experience significant head and flow rate reductions. These pumps are often installed with significantly oversized motors to overcome efficiency losses due to viscosity.
Screw pumps are increasingly popular in the midstream market, where their ability to handle high viscosities allows operators to pump at lower temperatures or use less diluent.
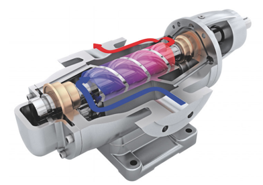
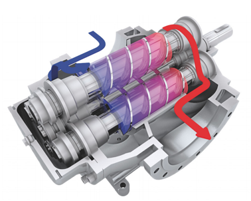
These pumps are hydraulically balanced, pulsation free and deliver a given volume from suction to discharge against the system backpressure. The pump has two rotors, one drive and one driven, and is reliant on the pumped fluid to fill and seal the area between the non-contacting rotors themselves and the liner. The pumped fluid seals each individual pumping chamber of the screw profiles, preventing back flow and loss of prime. The rigid rotor design, made from a single piece of bar stock, keeps the rotors from contracting the liner even at high pressure temperature.
The rotors are supported by radial bearings and the torque is transmitted from the drive to the driven rotor using a set of synchronizing timing gears. The timing gears and bearings are external to the process fluids and are oil lubricated by a lube oil system which could be either internal or external, depending on pump size and motor power.
The twin-screw pump has four shaft penetrations from process to the clean oil side, so at least four shaft seals are required. The seals are mechanical and supplied in either single or double seal configurations, depending upon the actual service, the process fluids and possible hazardous emissions. Single seals are typically used for straight oil/crude oil service, while double mechanical seals with barrier fluid systems are sometimes used. Cartridge type seals are helpful in connection with service and are often used.
Three-Screw Pumps
When lighter oil is pumped and when diluents are used to reduce viscosity in heavy oils, gas may flash, which can lead to vapor locking in the centrifugal pump. Low viscosity oil, API40 or lighter, can be economically and reliably pumped with three-screw pump as an alternative to horizontal ESPs. A high pressure three-screw pump is significantly smaller and has no thrust bearing or oil system to maintain.
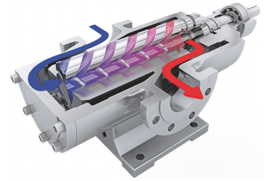
Screw pumps have extremely low fluid pulsation, removing the need for pulsation dampeners or complicated pipeline support systems as required by reciprocating pumps. They are also hydraulically balanced and operate well below any critical speed range, which guarantees low vibrations. Using VFD the speed can optimize for flow control depending on use, allowing for large savings on energy and service costs.
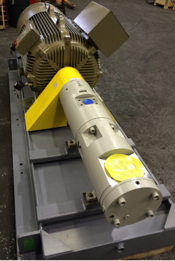
The three-screw pump’s main elements are three rotors (one power and two driven rotors), an externally lubricated bearing capable of handling thrust loads induced by high inlet pressure, a mechanical seal, a separate liner, an outer casing and a bearing/seal housing. The power rotor (coupled to driver) performs the pump work while the idlers act as rotating seals, sealing the individual pumping chambers. The torque is transmitted to the idlers by the driven rotors through rolling contact between the rotors. The pumped fluid creates a barrier between the rotating elements and the surrounding liner, preventing direct metal contact.
The liquid enters the pump and fills the first pumping chamber of the screw set. As the screws rotate, sealed chambers are formed, and the liquid is conveyed from suction to discharge. It moves a defined volume from suction to discharge lie a piston pump with an infinite piston stroke.
Conclusion
The operational flexibility, higher efficiency and robustness of modern screw pump designs have made them suitable for an increasing number of applications in the upstream and midstream market. A strong driver is the desire by operators to use rapidly shifting trends and monetize available opportunities in the supply and demand of different oil and gas products. Adding flexible screw pump technology to a facility increases the likelihood of taking advantage of such opportunities.